プラモってどうやって作られる?メーカー「青島文化教材社」に聞いてみました! 実際の製作工程やプラモの気になる部分を解説【模型質問箱】
2023.07.01みんなの気になる“模型の質問”に答えます!
読者の皆様からのアンケートはがきやHJ Web、SNS等にお寄せ頂いたご意見やご質問を参考に「気になる模型の質問」のプロモデラー・けんたろう、フミテシ、そしてホビージャパンモデラー陣やメーカー各社様がお答えていきます!
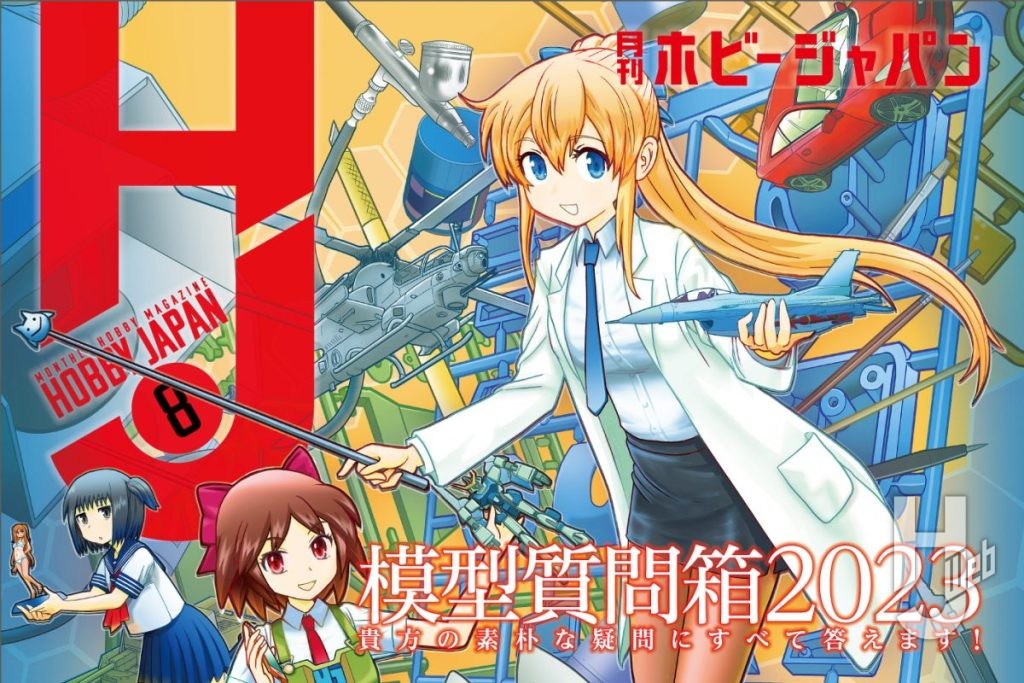
「月刊ホビージャパン8月号」好評発売中!
Q.プラモデルってどうやって作られているんですか?
A.プラモメーカーの人に実際に聞いてみました!
始まりました、模型質問箱! ひとつ目の質問から、なかなか一言で は説明しきれないものとなっていますが、この質問に全力でお答えするため、静岡のプラモメーカー「青島文化教材社」へ行き、実際にプラモデルを作っている方々に話を伺いました。当記事では、企画を始めるところから、データ作りや金型作り、最後の箱詰めまで、すべての工程にこだわりが詰まったプラモデルの製造工程「プラモデルができるまで」を解説します! 記事での工場見学をお楽しみください!
青島文化教材社ってどんな会社?
静岡市初の民間機パイロット・青嶋次郎氏が創業した青島文化教材社(通称:アオシマ)は、キャラクターキットもスケールモデルも手広く手掛ける古豪のメーカーです。ジャンルによってガラッと構造や組み方が変わる変幻自在の立体感で、簡単に組めるカーモデルからハードコアなキャラクター、そしてスケールモデルまで幅広く遊びのあるプラモデルを手掛けています。
❶企画
これをプラモにしたい! あれをプラモにしたら売れるかも? など、常にアンテナを張り巡らせて企画を練っています。カーモデルであれば企画をする段階で、自動車メーカー様に取材をお願いしたり、データを貰ったりすることまで考えます。海外の自動車メーカー様だと、貰えるデータが全くないものもあるので、実際に車を撮影しに行ったり、3Dスキャンをさせてもらったりしています。また、当然ですが最終的にはきちんと利益が出るようにしなければいけないので、試算をすることがとても大切です。こういった原価試算などの承認が下りて、自動車メーカー様のOKが出てようやくプラモデル作りをスタートすることができるようになります。
❷設計
プラモのデータを設計するときは、基本的にはすべてのスケールモデルで実車取材を行い、また取材などで得たデータをもとに製作します。実車からカーモデルを作る時だと、企画者とともに取材に行き、900枚くらいは写真を撮りますね。こんな感じで写真から立体にいちから作り上げることもあれば、今では3Dスキャン技術も進歩しているので、現地でスキャンしたデータをもとに設計したりしています。
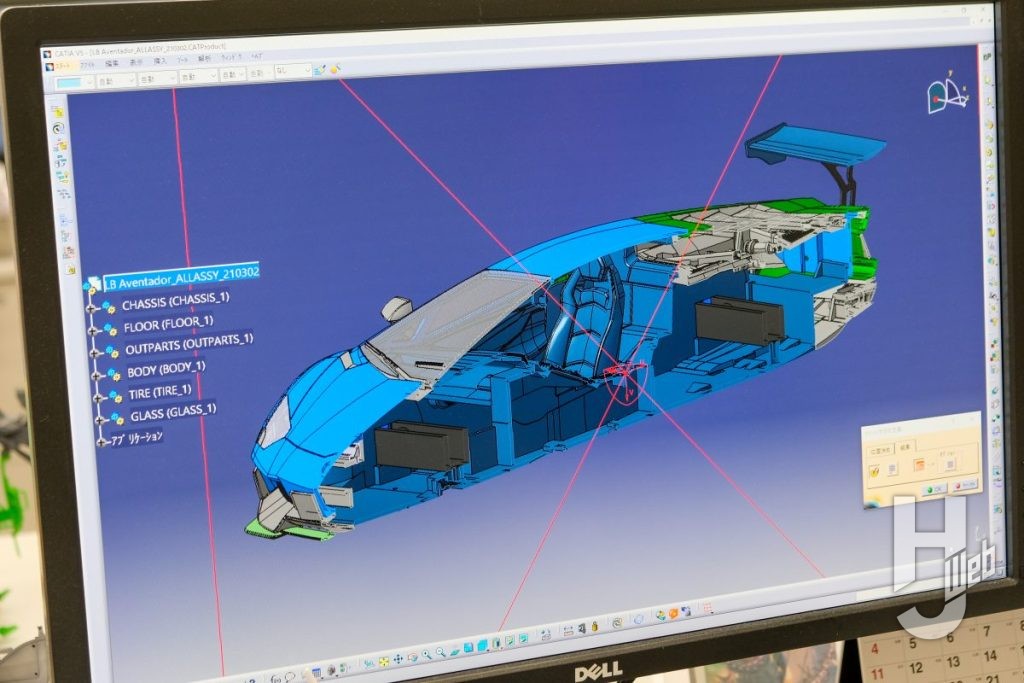
ただこういった3Dのスキャンデータは、外見は正確に再現されているのですが、レントゲンのような技術ではないため内部のデータは存在しません。そのため、この断面図を見てもらえるとわかるように、プラスチックの厚み(肉厚)を付けて、どこを合わせ目にして、どこまで作り込むのかという部分は企画担当と話し合って決める必要があります。例えば実車に、あまりにも細かすぎるパーツがあるとき、それを1/1から1/24スケールに縮小した場合どうしても金型では彫れず、モールドとしては消えてしまうのですが、それが特徴的なモールドであれば、あえてそれを少し大きく彫刻して違和感の無いように印象付けたりしています。他にも、ライトユーザーさん向けのものであれば組み立てやすさを重視し、車のドアをくっつけたり、逆にコアユーザーさん向けのものだと可動式にしてみたりといった、手に取ってもらえる方にとっていいものになるよう担当が決めたコンセプトに合わせてデータを作るのも設計の醍醐味です。
❸金型製作
プラモデルの金型は20年ほど前までは職人が木型を彫り、それをもとに金型を作っていましたが、今では加工技術の進歩もあってデータから直接金型を作ることができるようになりました。金型を彫る方法は、高速回転する工具で切削を行う「マシニングセンタ(CNC)」を使った方法と、溜めた油の中で銅の電極を通電させて形を加工する「NC放電機(EDM)」を使う方法のふたつが基本です。形作るパーツの大きさや形に合わせてこのふたつを複合的に使っています。
金型には「キャビティ」と「コア」があります
金型の秘密その① エジェクタピン
コア側の金型に設置されたたくさんの丸いピン。これはエジェクタピン(Eピン)と呼ばれ、プラモデルが成型し終わった後に裏からこのピンを突き出し、型からきれいに出力品を取り外すために設けられています。一見無駄とも思える、パーツの裏側にある丸いポコッとした模様や、ゲート付近のランナーから少し飛び出た様なプラの部分は、金型から造形物を取り外すときに必要なものとなっています。
金型の秘密その② 止めピン
今回紹介する金型では、ひとつの金型にすべてのランナーを彫刻しています。ただ、見てもらって分かる通り、ランナーごとに成型色が違うため、こういった場合は「止めピン」を使ってプラの流れをコントロールします。止めピンが出ているときは、そこに樹脂が流れないので、狙ったところだけにプラを流し込むことができます。1万個成型する場合、まずはグレーで出し、次に白、黒、クリアーと進めることになるので、4万回同じ金型で成型しなくてはいけないということになります。
❹射出成型
成型機には大きく分けて3つのユニットがあります。ペレット状の樹脂を溶かして型に注入する射出ユニット(写真手前側)、速度や圧力、温度や量を細かく設定できるコントローラー(写真中央のパネル)、樹脂が漏れないように約1tの圧力で金型のキャビとコアを締める型締めユニット(写真奥側)です。手順はまず、漏斗のような形状の投入口に樹脂原料を入れます。次に射出ユニットのシリンダーを約200度に設定し、溶かしたプラを練り込みながら型締めユニットに注ぎます。金型にプラが流れたらコア側を動かして型を緩め、Eピンを使って成型品を取り外します。
試作から量産までの険しい道のり
金型に彫られているすべての部品を金型通りの寸法に出力する必要があるため、金型が出来上がったあとでも量産を始める前に何度も試作(テストショット)を行っています。パーツ同士の嵌め合わせがきつかったり緩かったりしないか、成型色の色や表面のツヤに問題はないかなどを徹底的にチェックします。その日の外気温や湿度によっても左右されるシビアな工程ですので、生産が安定するまでは何かしらどこかで問題が発生してしまいます。そのたびに熟練の作業員が微調整を繰り返し、ようやく安定生産ができるようになります。
❺箱詰め
「プラモができるまで」の最後は箱詰めです。ベルトコンベアーで箱を流し、定められた順番でランナーを箱に入れていき、最後に重量をチェックしてパーツの過不足を確認すれば皆さんの手元に届く商品の完成です。アオシマだと、箱にパーツを入れる順番を指定することがあります。箱を開けたときに一番最初に目に入ってほしいのはこのパーツかなとか、最後はこのパーツが来るのがいいかなという企画担当者のこだわりを生産管理部と擦り合わせ、箱詰めの順番まで設計します。ですので、ユーザーの皆さんもそういった視点で箱を開けてもらえると、この担当者はこういう考え方で箱詰めしてるのかな、と楽しんでいただけると思います。
Q.プラモの成型色ってどう決められて、どうやって色を付けているんですか?
A.実物があればそれを元に色を決め、キャラキットはデコマスで色を決めます。着色は専用の着色剤を使用します
成型色とは、キットに使われているプラスチックの色のことを指します。この成型色はどのように決められているのでしょうか。また、どのように色が付けられているのでしょう。
この質問に答えてくれたのは、「プラモができるまで」を紹介してくれた青島文化教材社の酒井さんと吉川さんです。引き続き解説していただきました!
スケールモデルの場合
カーモデルの場合だと、実車のパーツやディーラーで販売されている車用の塗料を参考にします。成型色が決まる工程としては、原料メーカー様や原料着色を専業にしている加工業者様にサンプルのカラープレートを作成していただき、それをこちらで判定するという方法で進めています。
キャラキットの場合
実物が存在しないキャラ系のキットの場合、デコレーションマスター(通称デコマス)と呼ばれる彩色見本を作り、版権元監修を行います。その監修が済んだものから、成型色の調色に入ることが多いです。ちなみに調色は1色あたり大体3ヵ月くらいかかるので、色が多いキットの場合、並行して進めないと大変なことになります。
原料着色の様子
押出成型機を使い、ベースの原料と着色剤を融解させてプラを絞り出します。次に、押出成型機から出てきた熱いプラを水槽へ投入し冷却します。最後に、裁断機で小さくカットすれば皆さんがよく知っている色付きのペレットの完成です。
Q.プラモデルに使われる素材って同じなんですか?
A.異なります。代表的な素材を教えます!
原料の種類と使い分け
PS ポリスチレン
着色が容易で収縮率が低いため製造しやすく、ユーザー様にとっても切削や接着、塗装がしやすいということもあり、プラモに一番よく使用されている材料となります。また、PSの中にも耐衝撃性の高いHIと、透明度が高いGPがあり、当社ではそれらを複合して使用しています。
ABS樹脂
不透明な樹脂で、割れや熱に強く、硬い樹脂です。切削や接着、塗装はしづらいですが、成型したときにプラの表面にツヤが出るため、スナップキットの車のボディパーツにも採用されたりします。
PE ポリエチレン
ポリキャップの原料としてよく知られ、柔軟性があります。薬品に強く、接着や塗装には向きません。
POM ポリアセタール
耐摩耗性に優れ、寸法も安定するため、モーターを内蔵したプラモのギヤなどに使用します。こちらも接着や塗装には向きません。
ブレンディングで思い通りの素材、成型色を作る
プラモに使われる素材は、先ほど説明した通りですが、実際はこれら複数の素材をブレンディングし、価格帯やユーザー様に合わせて配合を変えています。そこに、Q.プラモの成型色ってどう決められて、どうやって色を付けているんですか?でも紹介した着色剤や着色済みのペレット(マスターバッチ、MB)をさらにブレンドすることで思い通りの成型色を作っています。
Q.パーツ表面にへこみが!これって何ですか?なぜ起こるんですか?
A.「ヒケ」と呼ばれるものです。プラスチックの樹脂が金型に流れて、冷えて固まるときに発生します。
パーツの表面に時々現れ、我々モデラーを悩ませる「ヒケ」。なぜこのようなへこみが発生するのでしょうか。また、どのような企業努力でヒケが出ないプラモを作っているのでしょう。
プラモデルに限らず、高い温度のものが冷えるときには必ず収縮が起こり、体積が減ります。ということは、約200度で成型されるプラモデルでも当然収縮が起きるわけです。ヒケが起きやすい場所で言うと、部分的にパーツが盛り上がっていたり、裏側に大きいピンがある場所はそこだけ冷めるのが遅くなり、ヒケが目立つことがあります。対策としては、プラの材質を変えたり、プラを金型に射出する速度や成型時間、外気温に合わせた金型の温度など、さまざまな条件を細かく設定して、なるべくヒケが出ないように品質を管理しています。
ただ、古い金型のキットだと、再生産するときにどうしてもヒケが出てしまう場合があります。50年前の金型だと、当時は全然ヒケを気にしないユーザー様も多かったのですが、技術の進歩もあり、常にユーザー様にとっていい商品を求めていった結果、ヒケはなるべく出さないものという現在の基準になっています。ですので、過去のキットでもなるべくヒケないようにしっかり条件出しをしたり、採算が取れれば金型を改造したりしてより良い商品を作る努力をしています。
Q.なぜ肉抜き、肉抜き穴というものが存在するんですか?
A.パーツの歪みやヒケを防止したり、樹脂の無駄をなくすためです。
大きいパーツの裏側や、アーマーの裏側などが1パーツで構成されているとき、裏側がスカスカになっていることがよくあります。このようなスカスカの部分を肉抜きと呼び、パーツに補強などが入って穴のように見える場合、肉抜き穴などと呼んだりします。なぜ、一見不必要にも思える肉抜きが必要なのでしょうか。
金型を使って、大きいパーツや分厚いパーツを一発で成型するのには限界があります。大きいパーツだとそのぶん形状が歪みやすかったり、分厚い部分では大きなヒケが発生したりと、安定した生産ができないことがあります。それでも、大きくて分厚いパーツを作る必要があるときに「肉抜き」が活躍します。
結局、肉厚を均一に保ちながら成型することが、一番不良品が出にくく、品質を管理しやすい方法です。そのため、成型上の都合でどうしても肉抜きを作らなければならないときがあります。そういった場合は、組みあがったときに肉抜きが見えにくくなるようにしたり、分割を変更してそもそも肉抜きが出ないようにしたりといったことを、担当者と擦り合わせながらその都度工夫して、完成したときにユーザー様にしっかり満足してもらえるように心掛けています。
TM & ©TOHO CO.,LTD